Polyurethane
A polyurethane coating can be a layer of polyurethane sprayed or cast onto the surface of a substrate to protect it from factors such as corrosion, wear, or weathering. We also manufacture products and spare parts in solid polyurethane or in combination with other materials to achieve the best properties.
Polyurethane is used when high demands are placed on durability, lifespan, and the potential for seamless coatings and repairs. It has high resistance to mechanical abrasion, is shock and noise-absorbing, and can vary from extremely soft and elastic to very hard and dimensionally stable. The material can exhibit a wide range of properties through various mixtures and curing processes during manufacturing.
We manufacture finished products or parts for products in solid polyurethane, but we can also cast a wear-resistant surface, for example, ceramic (alumina), with a steel core. An advantage of casting products in polyurethane is that the mold cost is relatively inexpensive since it doesn't need to withstand high pressures or vacuums, making production in small batches quick and straightforward.
Polyurea
Polyurea is a sprayable plastic coating with rubber-like properties that provide protection against wear, temperature variations, and moisture. This material is used as a waterproofing layer as well as for wear and corrosion protection and offers very high durability combined with high elasticity and an extremely fast curing time. One significant advantage is that polyurea does not react with water, allowing for the application of a waterproof layer on a surface that is not completely dry without affecting the material, although adhesion may suffer under such conditions. The product can also be applied in temperatures ranging from minus 10 degrees to plus 50 degrees Celsius.
Composite
We also manufacture composite products, ranging from a simple steel core coated with a thermosetting plastic to using five or more different materials to leverage the best properties of each material. The materials we use have varying hardness, ranging from 38 Shore A, a scale used for softer materials like rubber, all the way to the Rockwell scale, which measures the hardness of metals.
Rubber
Rubber coating provides a surface with high resistance to both corrosion and wear, significantly extending the lifespan of the substrate. The material is highly flexible and ensures a uniform layer thickness across the entire substrate. Rubberizing critical components continuously exposed to friction or other stressors is a long-term alternative. There are many different rubber qualities to choose from for protection against various environments, such as heat, abrasion, or chemicals like oils.
Today, we can offer a wide range of rubber options, including rubber with adhesive layers for application on steel, drum coatings with ceramics as well as diamond patterns, and a variety of rubber sheets in different qualities and hardness levels.
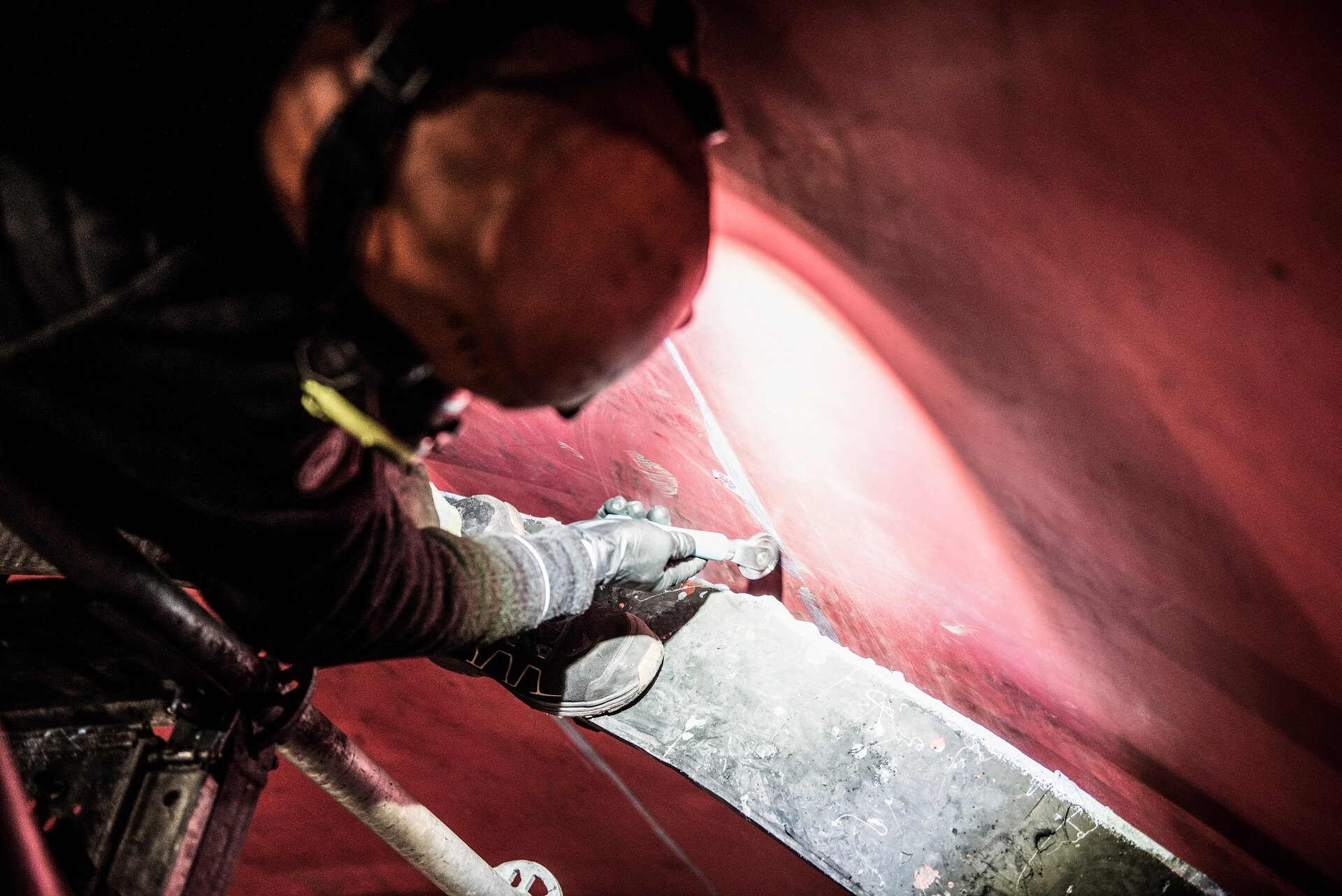
Ceramics
Primarily, we use ceramics with 92% aluminum oxide for a good balance between wear resistance and toughness. We can also cast ceramics in polyurethane as a shock-absorbing binder in a steel plate to facilitate welding. These products are referred to as "polykeram." Aluminum oxide is electrically insulating but has excellent thermal conductivity. Ceramics also possess good thermal shock resistance, high wear resistance, and high tensile strength.